Russia 3D Prints Satellite Antennas in Breakthrough for Space Manufacturing
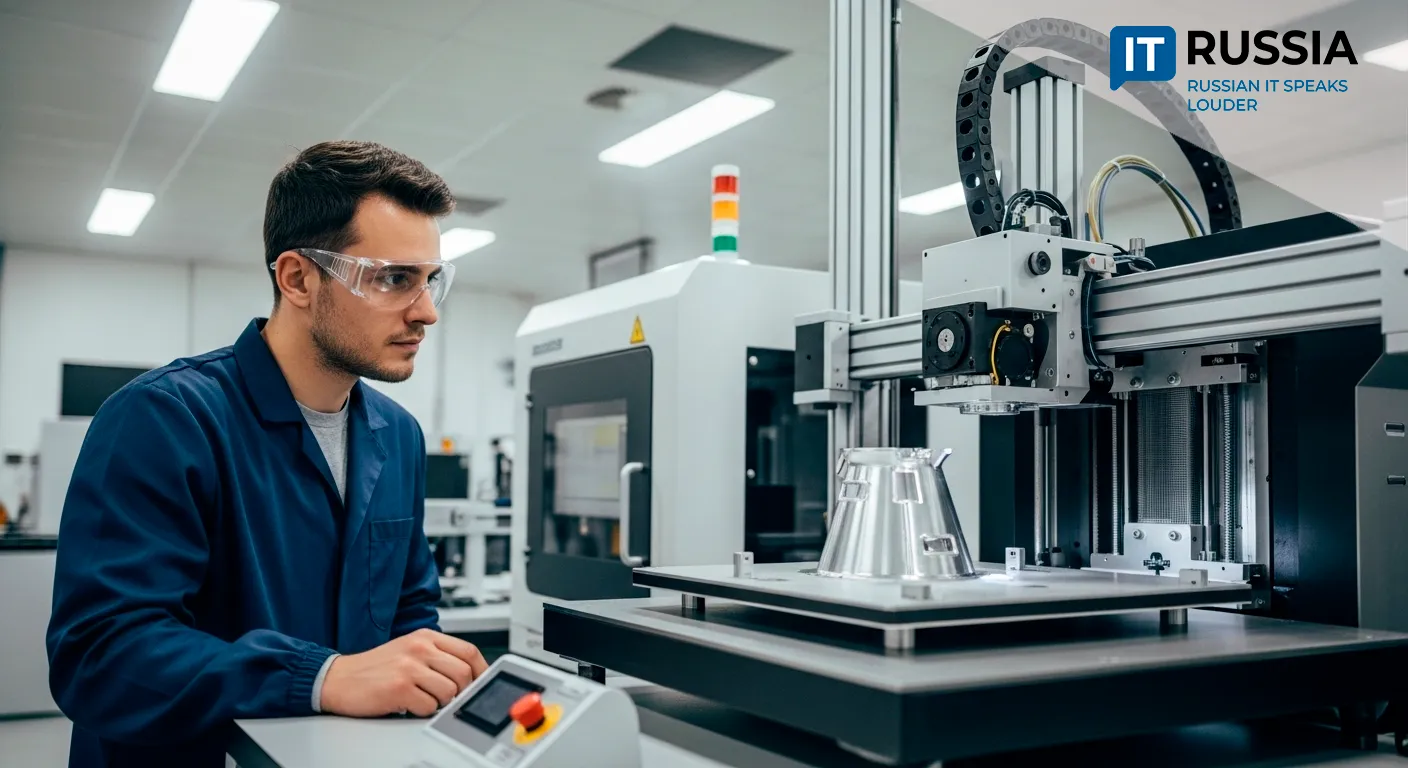
Russian satellite manufacturer Reshetnev is pioneering 3D printing for critical space components—starting with antennas, and aiming to reshape the economics of satellite production.
Faster, Smarter, Stronger
Russia’s Reshetnev Company, part of the
Roscosmos State Corporation, is moving quickly to adopt additive manufacturing
for satellite components—a shift that promises faster production, lower costs,
and higher reliability.
Using laser sintering of aluminum powder, engineers can now 3D print monolithic
satellite antennas layer by layer. These structures replace complex,
hand-assembled components made from hundreds of individual parts. Traditional
manufacturing could take weeks. 3D printing cuts it down to a matter of days.
And the benefits go beyond speed. Printed antennas are structurally stronger,
more resilient, and have fewer points of failure. For high-frequency
bands—especially millimeter-wave applications where even microscopic defects
can compromise performance—this precision is mission-critical.

Rethinking What Antennas Can Be
Reshetnev’s new approach also redefines
design constraints. Without the limitations of conventional machining,
engineers can explore entirely new antenna geometries. The result? Smaller,
lighter, and more efficient payloads optimized for space.
Additive manufacturing drastically reduces material waste, making the process
not only cheaper but more sustainable. As satellite operators face mounting
pressure to cut emissions and reduce launch mass, this matters.
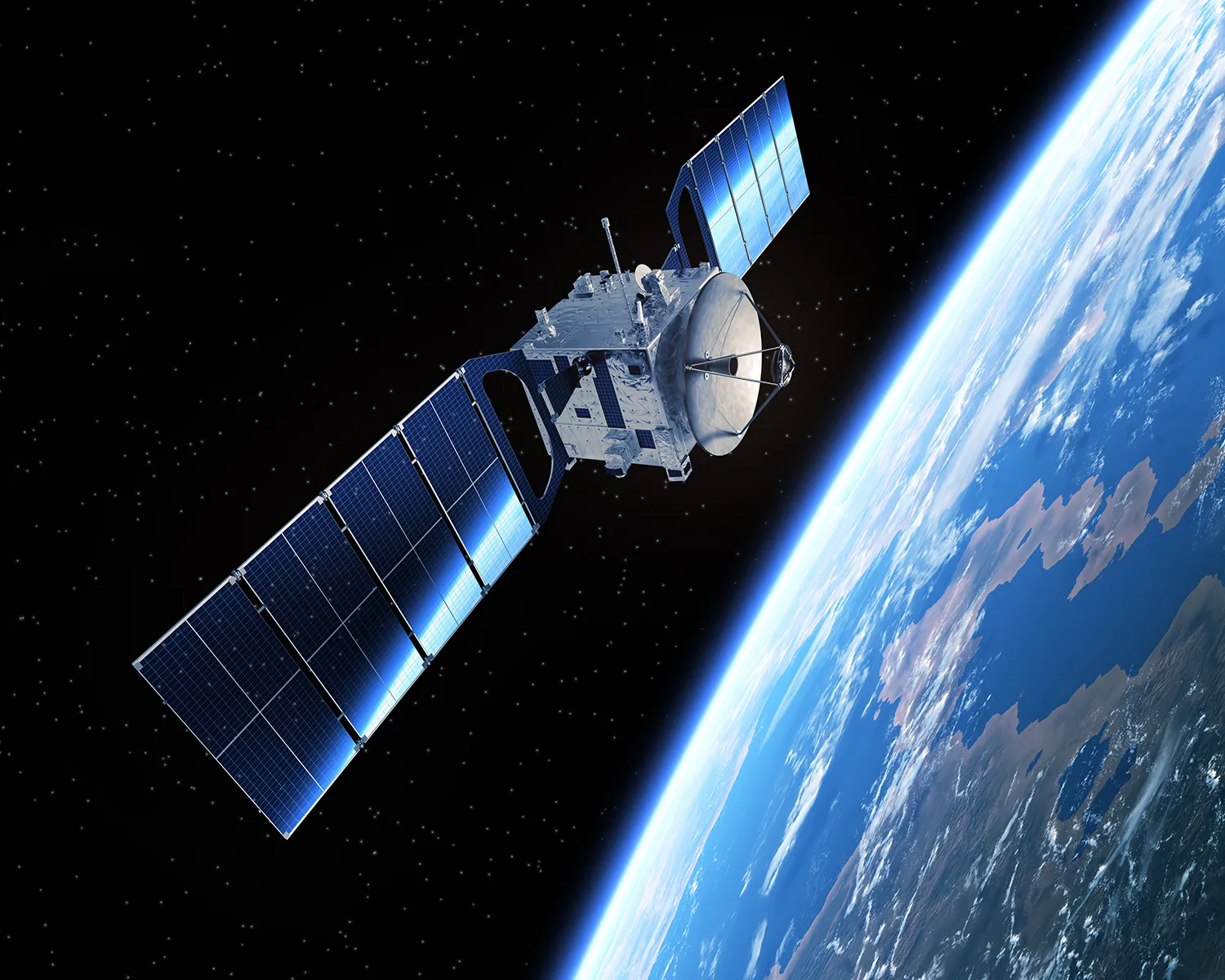
Beyond Antennas: A New Model for Space Hardware
While antennas are the first application,
Reshetnev’s roadmap goes much further. The same techniques could soon be
applied to print structural parts, thermal shielding, and even full satellite
bodies. For countries looking to bootstrap satellite capabilities—especially in
the Global South—this is a potential game-changer.
Russia sees significant export potential. The technology lowers the barrier to
entry for national satellite programs, offering a scalable path forward for
emerging space economies.
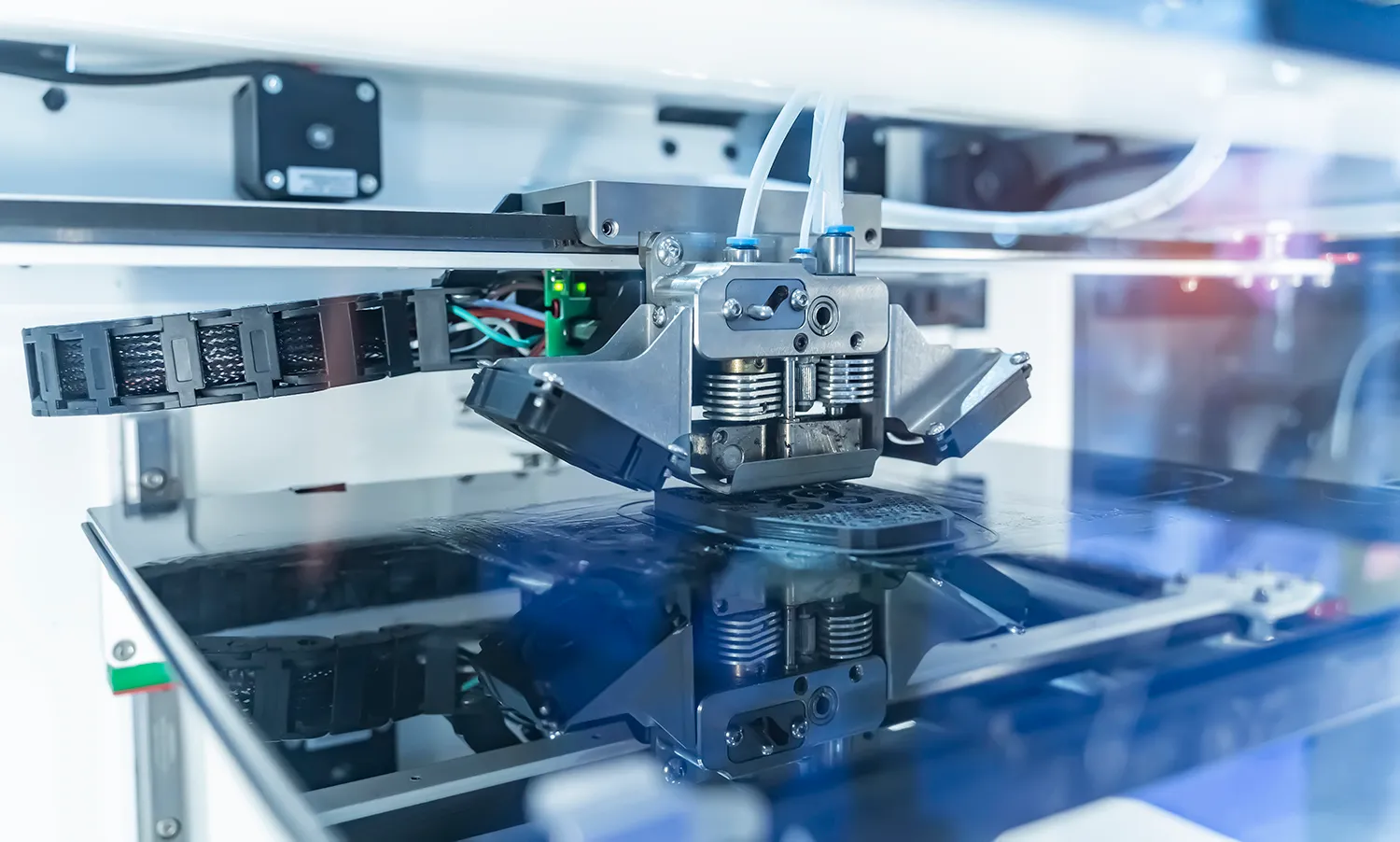
Decades in the Making
This leap didn’t happen overnight. Russia
has been investing in adaptive manufacturing for years. In 2018, Rostec
launched its Adaptive Technologies Center to integrate 3D printing across
aerospace and defense sectors.
By 2021, serial production of 3D-printed parts began for Russia’s PD-14 engine,
used in the MC-21 passenger jet. In 2023, Irkutsk National Research Technical
University unveiled 3D tooling for composite manufacturing at the Irkutsk
Aviation Plant.
Today, those innovations are finding their way into space. As engineers embrace
lighter, stronger, and more flexible manufacturing methods, Russia positions
itself not just to keep pace—but to shape the next standard.