Russia Develops Domestic Equipment Industry for Semiconductor Production
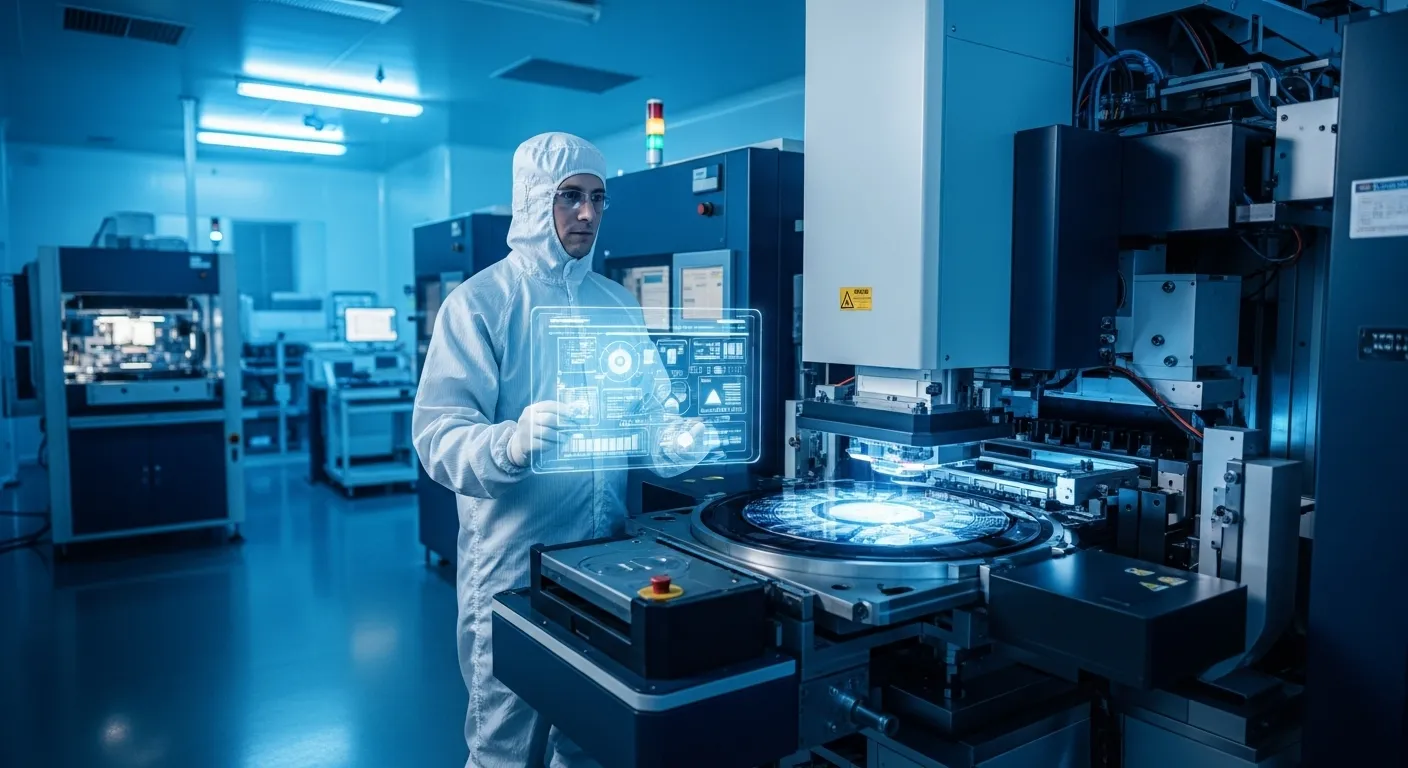
Despite ongoing sanctions pressure, Russia is on track to meet its domestic demand for baseline microchips by 2027–2028 and for critical semiconductor components by 2030.
Massive Microelectronics Development Program
Under a large-scale national initiative, Russian microelectronics companies are expected to receive around 122 pieces of domestically produced equipment by 2030–2032. These systems cover crucial manufacturing stages, including photomask design, plasma-chemical etching, and epitaxy. The project will involve more than 110 research and development efforts (R&D), with an overall budget estimated at $1.26 billion through 2027.
Three key R&D efforts have already been completed. These include the 'Progress PPI' project for projection imaging onto wafers at 350 nm resolution, developed by ZNTC from 2021 to 2024, and the 'Progress KTF' project for photomask topography inspection.
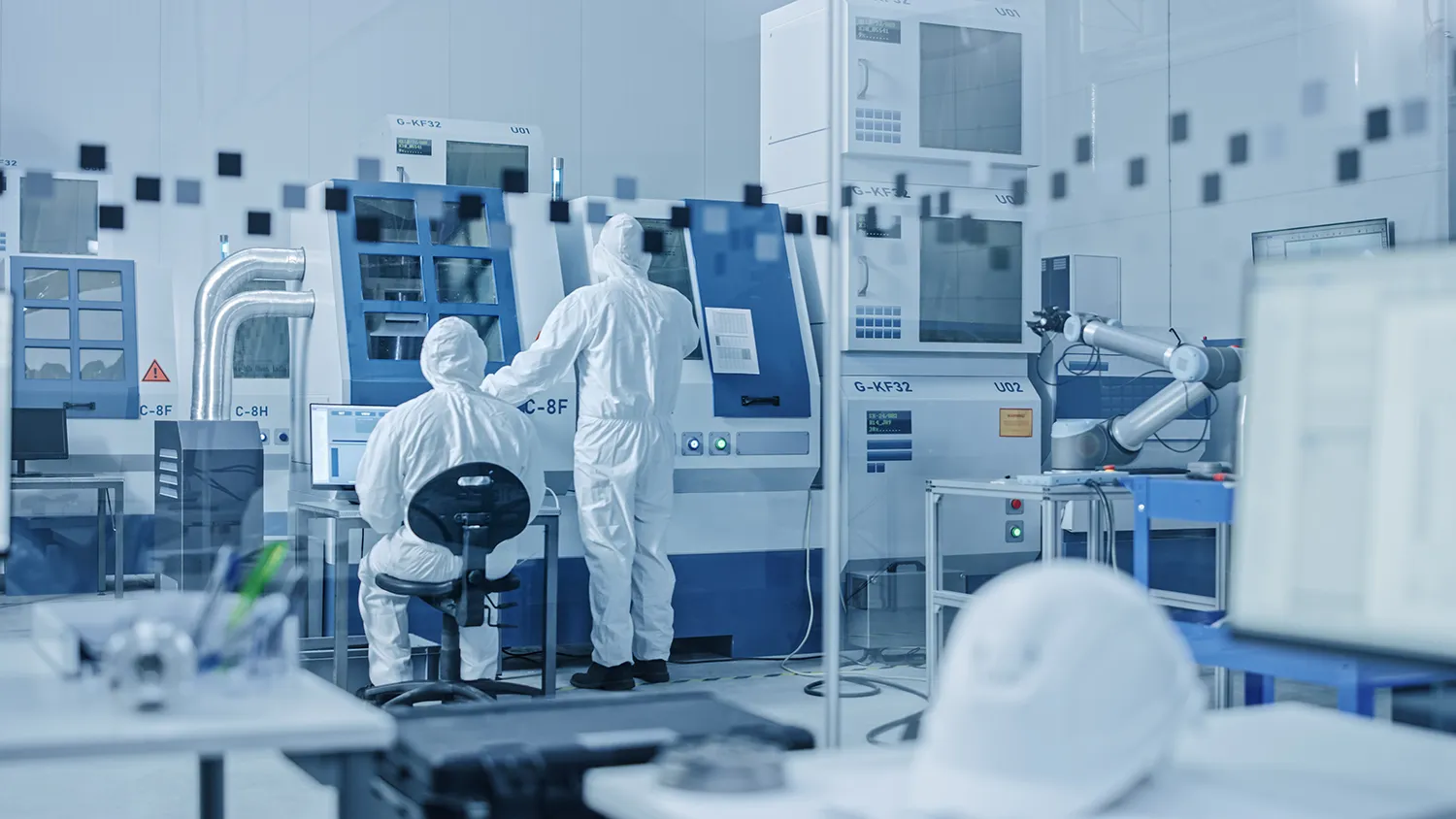
Nine additional units are scheduled for completion in 2025. These include a molecular beam epitaxy system by JSC NTO, automated high-frequency testing equipment by RTU MIREA, a plasma-chemical etching cluster by JSC NIIME, and a crystal growth system for germanium substrates.
Experts estimate that by 2030, thanks to aggressive import substitution, 70% of the equipment used in Russia’s semiconductor industry will be domestically manufactured.
Building a Local Resource Base
Russia is also establishing its own resource base for advanced semiconductor materials like synthetic diamonds, germanene, and graphene. These materials may eventually replace silicon entirely or partially, giving Russia a strategic edge in the global microelectronics arena.
A major priority is the development of lithography technologies. By 2026, Russia aims to roll out ultraviolet lithography systems at 350 nm and 130 nm, and electron beam lithography at 150 nm. If successful, this would position the country among the few nations capable of producing homegrown chipmaking equipment, alongside global leaders like ASML.
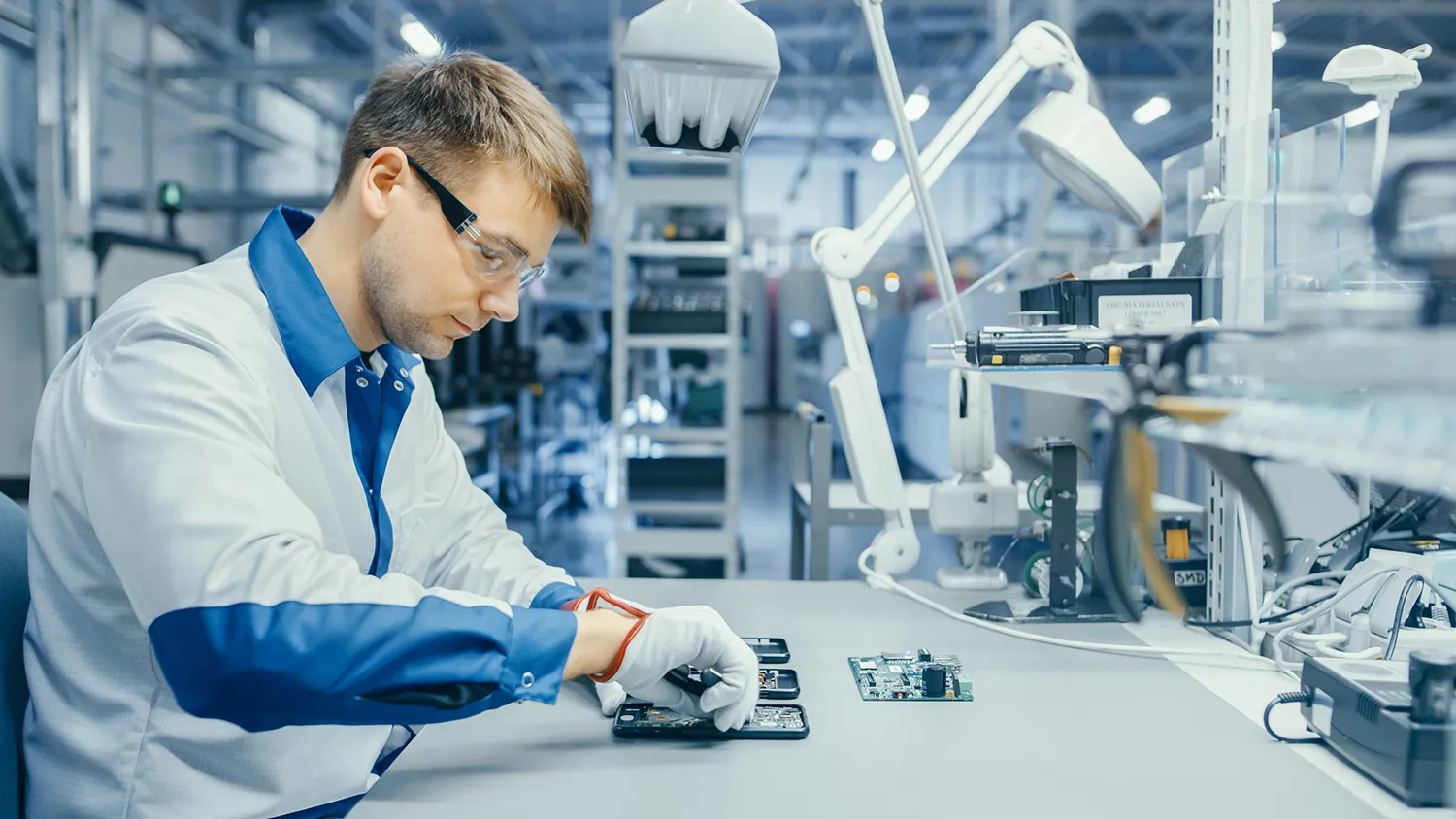
Scaling the Industry
Leading Russian companies such as Mikron, NIIME, and Tekhnotekh are actively modernizing production lines and acquiring new equipment. A robust innovation ecosystem is taking shape with over 250 projects in specialized materials, 313 in chemical reagents, and around 216 in computer-aided design (CAD) systems. This infrastructure is critical for scaling up domestic chip production.
According to the national roadmap, the first 12 units of equipment will be delivered in 2025, followed by another 57 in 2026.
Mastering Critical Chip Manufacturing Processes
Russia has developed its first plasma-chemical vapor deposition (PECVD) system for 300 mm silicon wafers—a global standard for chip fabrication. Previously, domestic systems were designed for 200 mm wafers, while most advanced microchips worldwide are produced on 300 mm substrates. This innovation, developed at the Research Institute of Precision Engineering (NIITM, part of the Element Group), will reduce costs by increasing chip yield per wafer.
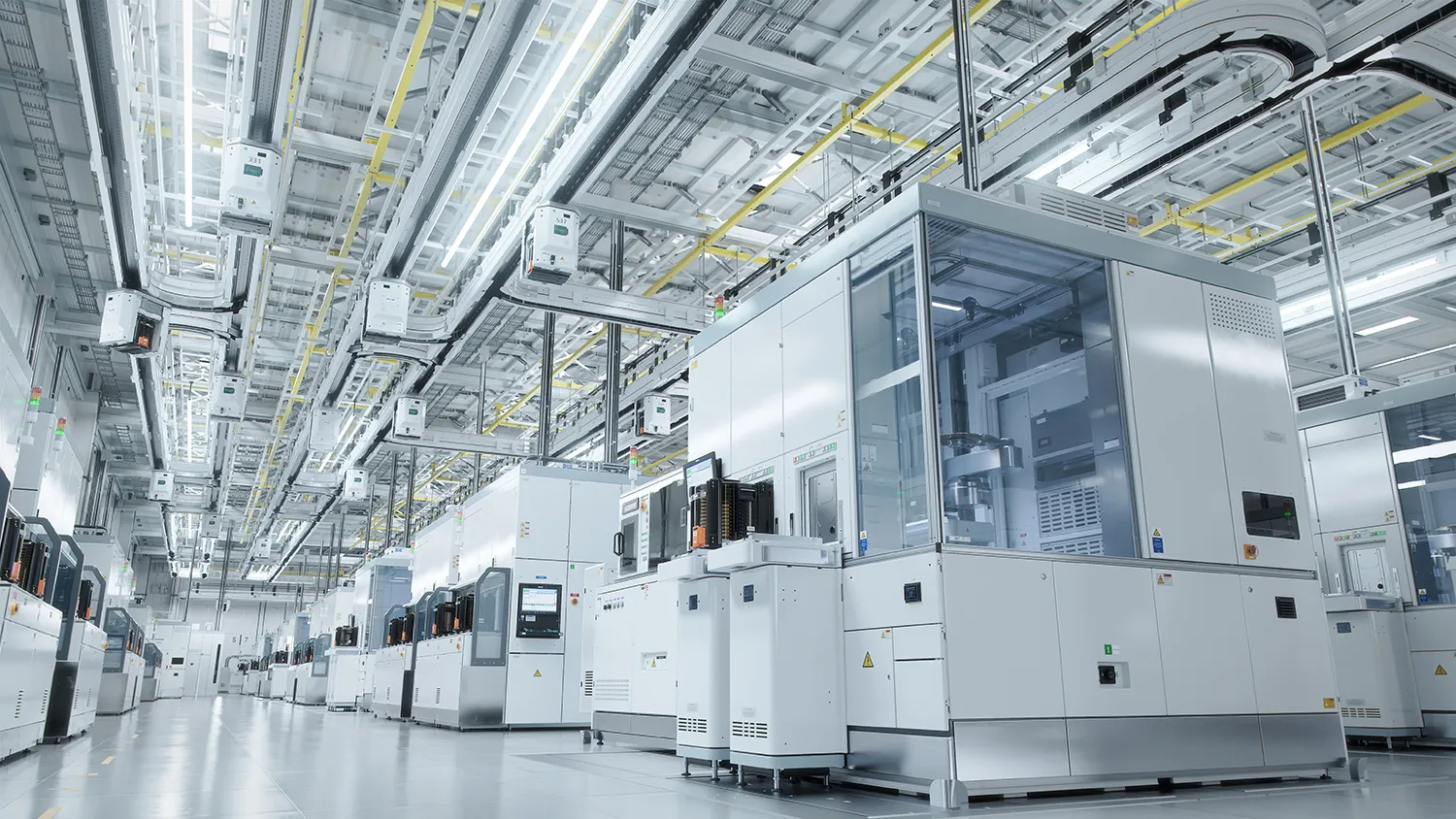
In 2024, the country also unveiled a demonstrator for a 350 nm lithography machine, with a plan to move to 130 nm technology by 2026.
Toward Technological Sovereignty
Although Russian technology is currently limited to 350–65 nm nodes—far behind global leaders working at 7–5 nm—these nodes are more than sufficient for basic applications such as controllers, RFID tags, and IoT devices. Experts believe that it will take at least another decade before these entry-level chips are replaced by more advanced solutions.
The national development forecast calls for a gradual increase in both output and quality of Russian-made semiconductor equipment. Full localization of technologies for nodes down to 65 nm is expected, along with potential exports to friendly nations. In the long term, Russia plans to advance to more refined processes at 28–14 nm.
Developing in-house semiconductor production will grant Russia technological sovereignty and long-term independence in its electronics industry.